Why Concrete for an Industrial Floor
Concrete floors, whether used in a residential home, a grocery store or a manufacturing plant, are basically the same.
In commercial or industrial settings, though, the concrete slabs usually have special requirements based on the loads or flatness or levelness required. To get a concrete slab that meets these requirements, NXT Concrete uses special techniques in pouring and finishing the concrete. Commercial or industrial floors can also have special requirements for surface hardness, finish, and even color. Wal-Mart, for example, has specifications for their exposed concrete floors that incorporates color, surface densifiers, and even a hard troweled finish.
Commercial / Industrial floors can be built on grade or can be suspended. Suspended floors are often built on metal decking, which is corrugated sheet metal supported by structural steel. Achieving high flatness and levelness values on these floors can be difficult since the decks and frames deflect under the weight of the concrete.
Commercial or industrial floors tend to be large surface areas that are susceptible to damage and cracking. A lot of that can be controlled by using the right materials in the mix designs. The key is to use the largest possible aggregate (since aggregate can't shrink), to get a well-graded aggregate (meaning there is aggregate of every size from larg- to small), and to use the lowest water content possible.
The timing and finish work done by
NXT concrete are also critical to getting a good concrete slab and there is a certain amount of planning and prep needed to accomplish these equally important goals of a durable floor.
Here are a few important points:
- The maximum size of coarse aggregate should not exceed 3/4 the minimum clear spacing of the reinforcing bars in structural floors, or 1/3 the thickness of non-reinforced slabs. Aggregates as large as 1.5 inches, though, can often be used.
- Fly ash or slag cement commonly appears in commercial or industrial floors. These materials (along with silica fume) are called supplementary cementitious materials or pozzolans and have various purposes.
- A material sometimes used with commercial or industrial floors is expansive cement (also called shrinkage-compensating cement). Shrinkage-compensating concrete expands slightly while setting then shrinks back to its original size. When done properly this can eliminate cracking and increase the spacing of control joints, but it requires an experienced concrete contractor and ready-mix producer to get everything to work properly.
- Hard, wear-resistant aggregates such as quartz, emery, and traprock, as well as malleable metallic hardeners, are frequently used as surface treatments in commercial or industrial floors. They are applied to the top surface as dry shakes and finished into the surface of the floor to improve the abrasion resistance of the surface.
- Concrete reinforcement comes in various types, these include welded wire fabric (mesh), steel reinforcing bars (rebar), synthetic fiber reinforcement (0.75 to 1.5 pounds/cubic yard), and steel fibers (34 to 68 pounds/cubic yard). Synthetic fibers, commonly polypropylene, are primarily useful for preventing plastic shrinkage cracking. Some fibers, such as steel fibers, can improve concrete flexural strength.
All concrete slabs poured directly on the ground require good and uniform sub grade or base beneath to support the concrete. Soft spots are the death of any slab. Here are a few things to keep in mind about the subgrade (the ground beneath the slab) and the subbase (an optional compacted gravel layer between the concrete and the subgrade):
- Grading of the subgrade—or rough grading--should meet a tolerance of +0 inch/–1½ inches.
- Base tolerances—or fine grading--should meet a tolerance of +0 inch/–1 inch for floor Classes 1 to 3 and +0 inch/–3/4 inch for floor Classes 4 to 9.
- The base material should be a compact-able, easy to trim, granular fill that will remain stable and support whatever equipment may be used on it. This can be stationary machinery or even forklifts or construction equipment driving over it.
- Vapor barriers are essential beneath most interior concrete floors, especially if there is any intention of installing moisture-sensitive floor coverings (tile, wood, vinyl, etc.). In general, the vapor barrier should be directly beneath the concrete.
- Whenever possible, NXT Concrete will install floor slabs in a controlled environment. Ideally the roof will be on and the walls in place—protecting the soil support system and the concrete slab from wind, rain, sun, and extreme temperatures will greatly improve the concrete slab.
What are waiting for? Contact
NXT Concrete to learn more about how our company can help yours!
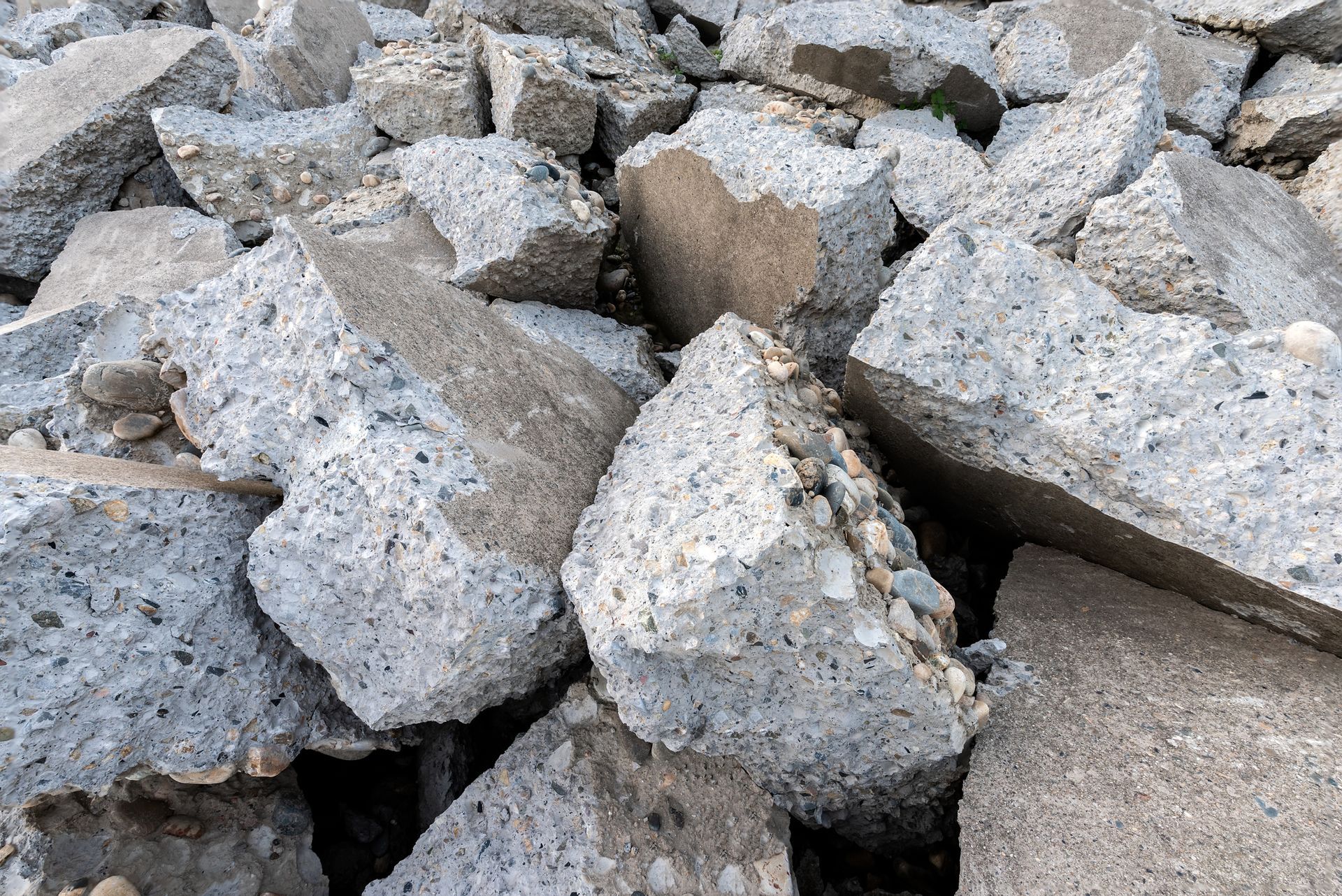
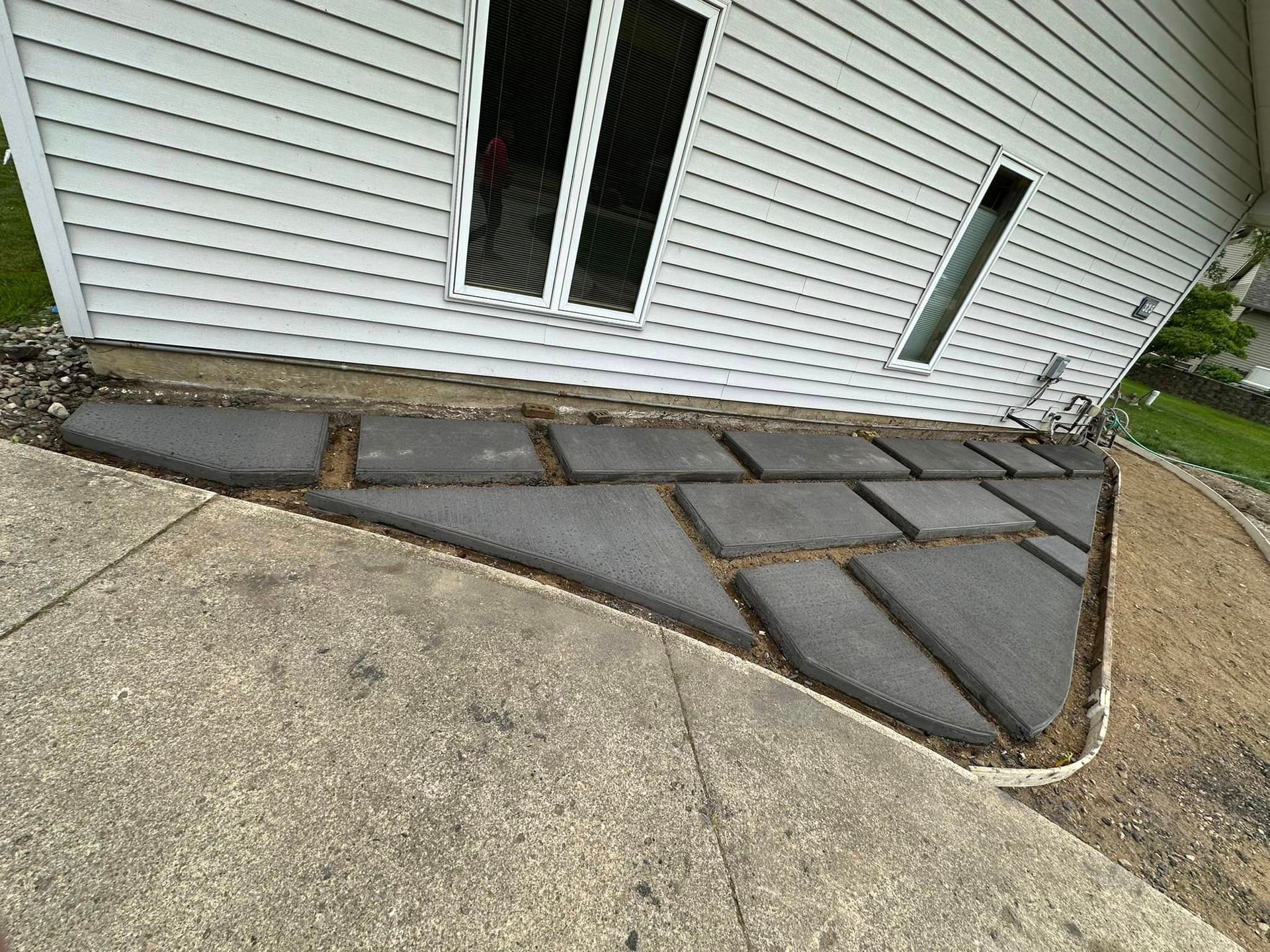